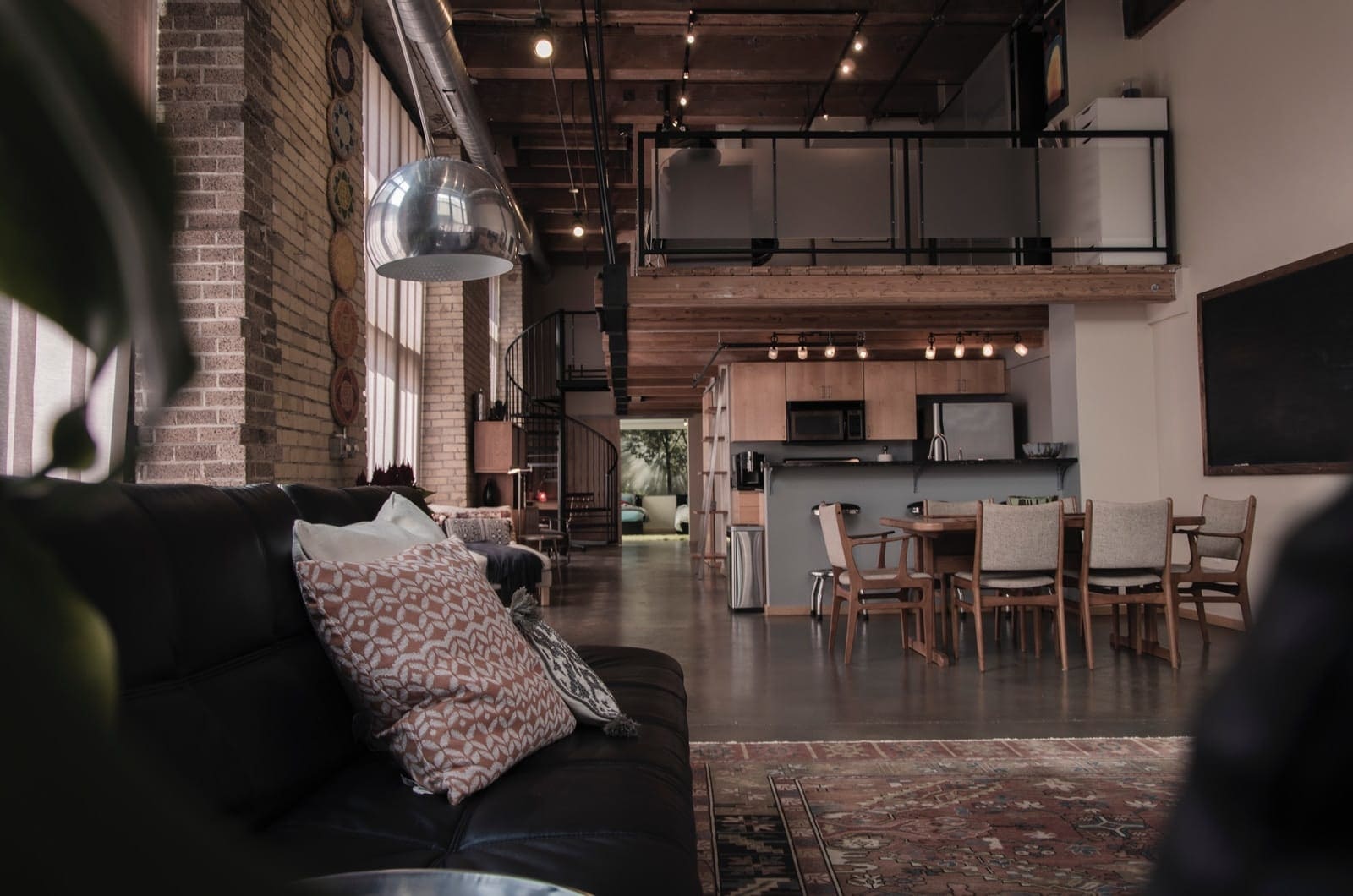
To begin, let me define what a “mezzanine” floor is. Mezzanine comes from the Italian name mezzano, which literally means ‘middle.’ The mezzanine floors serve as a center or additional floor in this case. While AW Structures use this term to describe extra levels in residential buildings, for the purposes of this discussion, a ‘mezzanine’ refers to extra floors in industrial or commercial residences.
When searching for a place to add more floor space
If considering a location for extra floor space, it’s critical to make sure that space follows the layout criteria In particular, an intermediate floor may be inserted with a ceiling height greater than 4.5m, but the physical design depth of the structure must be considered. i.e. there must be 2m of clear headroom over and under the mezzanine level, so a construction depth of more than 0.5m could cause problems.
The products used to suspend the mezzanine are included in the building depth. The total scope of work is typically created by combining a main beam with the decking. Later in the post, I’ll return to these elements.
The level on which the mezzanine will be constructed
In addition to the height, the sub-level, such as the floor on which the mezzanine will be constructed, must be regarded. This should be able to support the weight of the mezzanine columns. Mezzanine floors are typically fixed on top of cement slab floors. Prior to construction, structural calculations demonstrating that the slab can withstand the point loads are needed as part of the local government building regulations submission.
When building specifics are unavailable, core samples from the slab can be taken and ‘crush’ examined to assess the concrete’s physical strength.
You can start designing a mezzanine floor for your location once these two conditions are in place. The distance between the columns (supporting pillars) is the first thing to determine. This is essentially determined by the slab measurement, which will reveal the maximum allowable load down a column as well as any obstacles along the way, such as floor joints, equipment, and doors.
If the place is fully free of obstructions, it may be a good idea to build the mezzanine floor from a financial standpoint ensuring that the columns are arranged in the most cost-effective way possible. The size of a standard economical design varies depending on the manufacturer, but a 4-meter grid pattern in both directions is very popular.
On mezzanine levels, there are a variety of decking materials to choose from
On mezzanine floors, there are a variety of decking materials to choose from, but chipboard is by far the most popular. The chipboard is unfit for a few conditions, including damp or wet workstations, as well as places with extremely high point loads. Durbar or chequer plate are two other forms of flooring that are both solid but loud and costly. Open grates enable light to pass through, but they are also loud and challenging to use with picking trolleys.
Conclusion:- Any open edges of the mezzanine, that is, sides of the floor that do not butt up against a wall, should be covered. Handrails are the most common method of accomplishing this. To prevent kicking something off the floor, a knee rail and, in most cases, a toe rail must be added in addition to the handrail. Handrails are subject to legislation, which should be followed.
Be the first to comment